The sprawl of Los Angeles isn't the most obvious of places to encounter a rocket factory, but tucked away next to Hawthorne Municipal Airport is the apt address of one Rocket Road, headquarters of SpaceX. It was here where I hopped out of my Uber near the base of a huge stage one booster from a Falcon 9. The sun was setting majestically behind it.
I later found out that this wasn't a prop, it is in fact a piece of very recent space travel history. When I got closer, I saw it was covered in scorch marks and looking a little grubby and for good reason; it was the first ever booster ever successfully recovered from a launch, flying (falling with style?) back to earth and landing itself upright on a platform. Smart.
Whether that sounds impressive or not, it's a fundamental reason SpaceX has managed to establish itself against entrenched incumbents like Boeing, Lockheed Martin and NASA. It's a lot more cost efficient to develop reusable rockets than one trick ponies. At the time of my visit SpaceX had some 50 missions scheduled delivering all sorts of cargo into orbit - from commercial satellites to resupplying the International Space Station, offering rates that significantly undercut their competition.
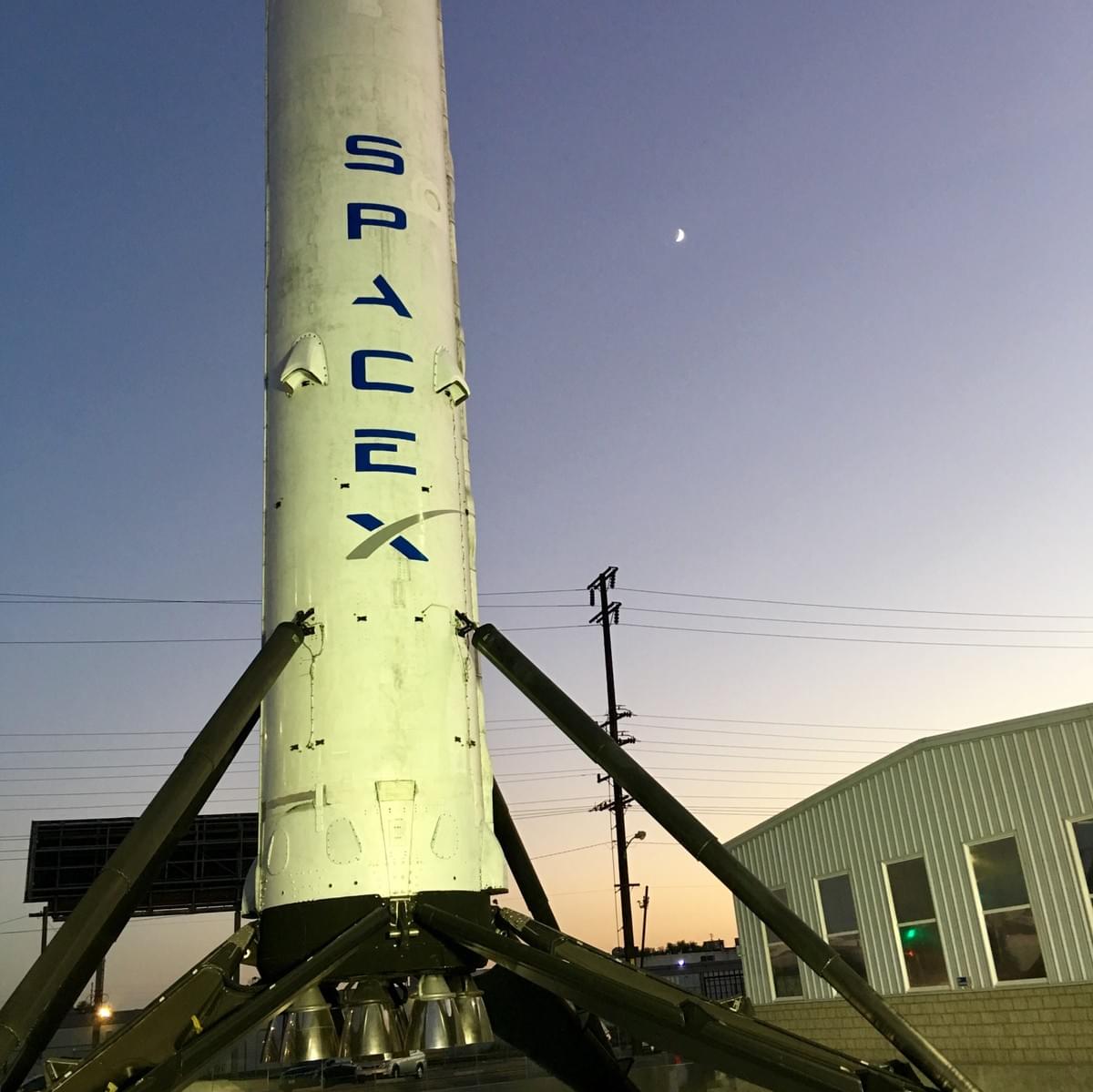
This was already a large part of my excitement of securing a visit. I take a lot of interest in speaking to those who work on disruptive technologies and changing the rules of the game, as it's something of my own passion and work with energy storage. I think there’s a lot of value in knowledge transfer that occurs in mixing with those from other sectors, and SpaceX was high on my wishlist firstly because I completely ‘get’ Elon's mission to make us an interplanetary species... and not in the distant future.
A second important reason was I figured there was also a lot to be learned about how SpaceX organised themselves with their Silicon Valley lean start up approach and how they scaled. On the back of my past interactions and visits with others like Google, Uber, Facebook etc I was really interested in seeing how Silicon Valley principles would apply to an industry that involved real hardware.
About a month before my visit Elon Musk had outlined SpaceX's vision in edifying detail. SpaceX wasn't just about becoming an established commercial space company (in itself an astounding feat having started from scratch in 2002) but rather focused on a much loftier goal; making humans an interplanetary species and creating a permanent colony on Mars. Well, for starters anyway.
So, what did I learn?
1. Don't just turn up
You can't just turn up and knock on the door and ask for a tour, if that's not already extremely obvious. It isn't a theme park, it's a real life high tech production line churning out rockets. I had to do a lot of asking around before I found someone in my network that could call in a favour and get me a visit. I got the ok just in time, once we had cleared up I wasn't a Russian spy or trying to sell them something (because of the government supply contract with NASA, SpaceX isn't actually allowed to source stuff outside the US except in special circumstances).
I had to undergo a full background check and get security clearance at least 10 working days in advance and whilst there I was strictly escorted. Also, I wasn't allowed to take photos inside, for obvious reasons. The indoor factory photos in this article are all stock pictures found from the internet, but I hope they get the point across.
It's also not uncommon to find Elon himself about the place. He frequently flies in on his jet I am told to check in on progress. I have a suspicion I may have been only a few meters from the man himself, as I was taken past his office at one point (and we were politely and firmly told to come back a different way by the lady manning the reception).
2. SpaceX: a grown up lean startup
Free professional barista coffee and ice cream. Ok, so perhaps it's a little gimmicky, but it's a sign to SpaceX's roots. Daniel (my guide) stopped me off at the SpaceX canteen where they serve a wide range of subsidised and delicious looking food. It all used to be completely free and also stocked beers in the fridges once, he told me, before the employee headcount (over 4000 and growing) got a bit too unwieldy to make this sustainable.
More seriously, SpaceX still exhibits a lot of the characteristics of its Silicon Valley-esque origins. The median age of its workforce is still in the twenty-somethings, it tries to develop as much of its technology in house as possible to avoid markup and to significantly drive down cost. There are plenty of examples where SpaceX have done this successfully (see the bestseller Elon Musk: Tesla, SpaceX, and the Quest for a Fantastic Future by Ashlee Vance).
The critical difference to me, and a reason SpaceX should be viewed with some reverence, is that it took this start up philosophy to an industry that requires actual hardware. All credit to companies like Instagram, WhatsApp, Linked In and the plethora of others, but challenging an incumbent industry with a physical product and applying that same philosophy is really not easy (Facebook and Google have started to progress a little more into the physical product market, so I'll give them a hall pass here even though the jury may be out on their success). SpaceX engineers and technicians work closely together, with management offices directly overlooking the production floor, each with visibility of the other.
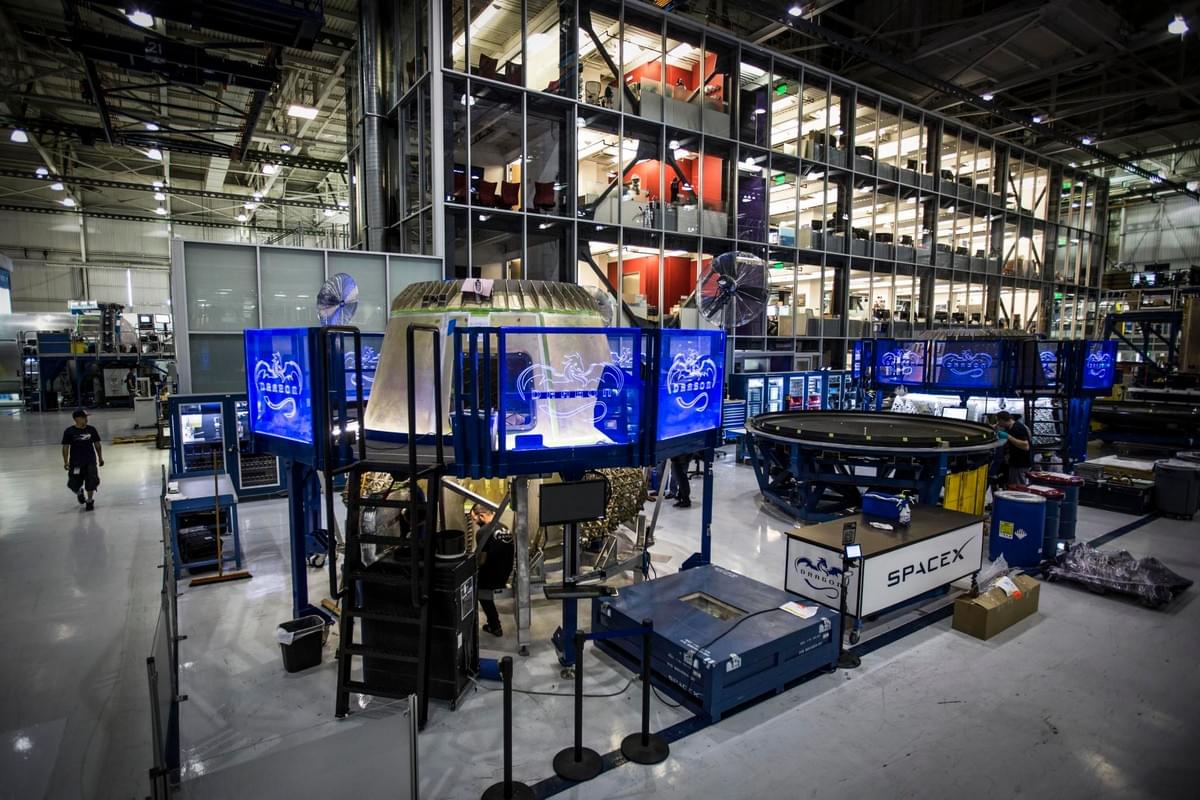
3. Hawthorne, we have a problem
One of the first things you see as you walk into the rocket factory is Mission Control, twice. There's the main mission control, with a floor to ceiling glass panel overlooked by the canteen where employees will gather to watch the launches to Cape Canaveral in Florida. There's also a second 'in case things go screwy' one that services as a fully redundant back up from the first, albeit a bit more tucked away down the corridor.
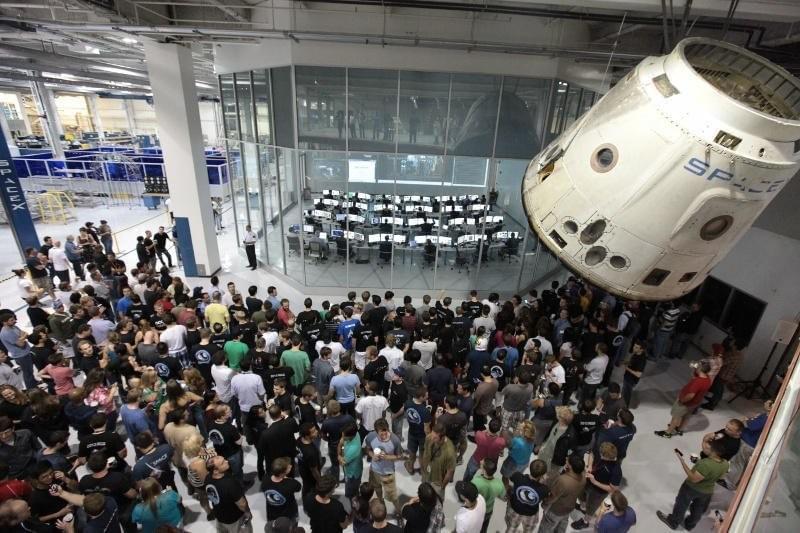
SpaceX employees still cluster around the canteen area behind mission control to watch the launches. Not every launch has been a success, with a recently an 'anomaly' resulting in a rather expensive Facebook satellite exploding on stand. Elon Musk famously almost burned through all of his Paypal cash in SpaceX's early days before finally producing a successful proof of concept, but his determination has paid off, and since beginning the company has to date completed 32 successful missions and is well on its way to establishing itself as a successful commercial space company, something that many people doubted would be possible.
4. Building rockets at rocket speed
The Rocket Factory is a 24/7 production line, consisting of 2 x 10 hour shifts and 4 hours down time for maintenance. It's a slick operation, churning out a full Falcon 9 rocket every 14 days at present (or a Falcon Heavy - which is basically 3 x Falcon 9s put together - every 6 weeks). Whilst already impressive, Daniel told me that the aim was to cut this down to 10 days with further advances and refinements to the process.
One of the key innovations of SpaceX has been to pioneer horizontal servicing of the rockets, which saves time and cost over a vertical platform where people have to clamber up and down rigging. Booster stage rockets are laid out on large rotary bearings, allowing it to be turned to face to person working on it rather than having them contort in all sorts of ways to reach the part that needs attention. Not only is this quicker, it's also safer and cheaper and makes it far easier to get planning permission for your production line I imagine, as skyscraper size factories are not welcome everywhere.
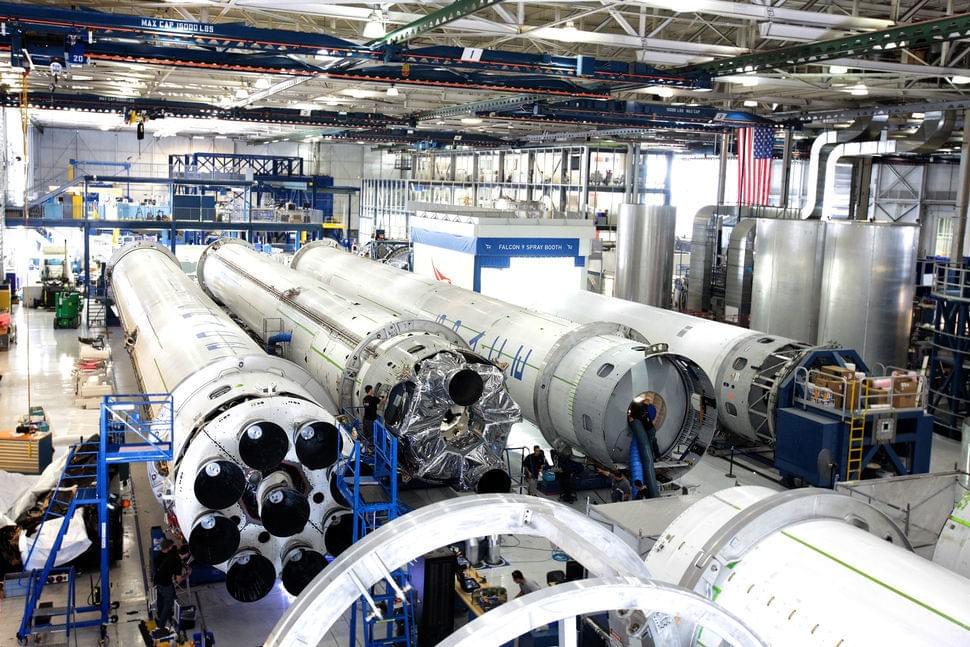
A whole host of other innovations have come out of refining the production facility. Another pointed out to me was that rather than having to do manual inspections over the chassis of a rocket for any micro-hairline fractures that could lead to a structural failure, SpaceX engineers have developed an automated detection technique with a sort of laser ultrasound scan that does the same job an order of magnitude faster and cheaper. Initially more expensive, but it pays off quickly.
Another thing the SpaceX engineers work very hard at is cutting down weight, which is crucial to overall efficiency and increases the payload capability of a mission. The stability legs of a Falcon 9 are carbon fibre, and whilst I was there they were also working on a new carbon fibre fuel tank.
5. Getting rockets from A to B is not easy
Once a rocket has been built there's still a problem. Getting it from LA on the West Coast all the way to the launch pad in Florida on the East Coast, a 2,500 mile journey even by the most direct or routes. The problem isn't that, it's that a Falcon 9 is around 70m long. Driving one of these beasts down the Interstate 10 isn't a straightforward process.
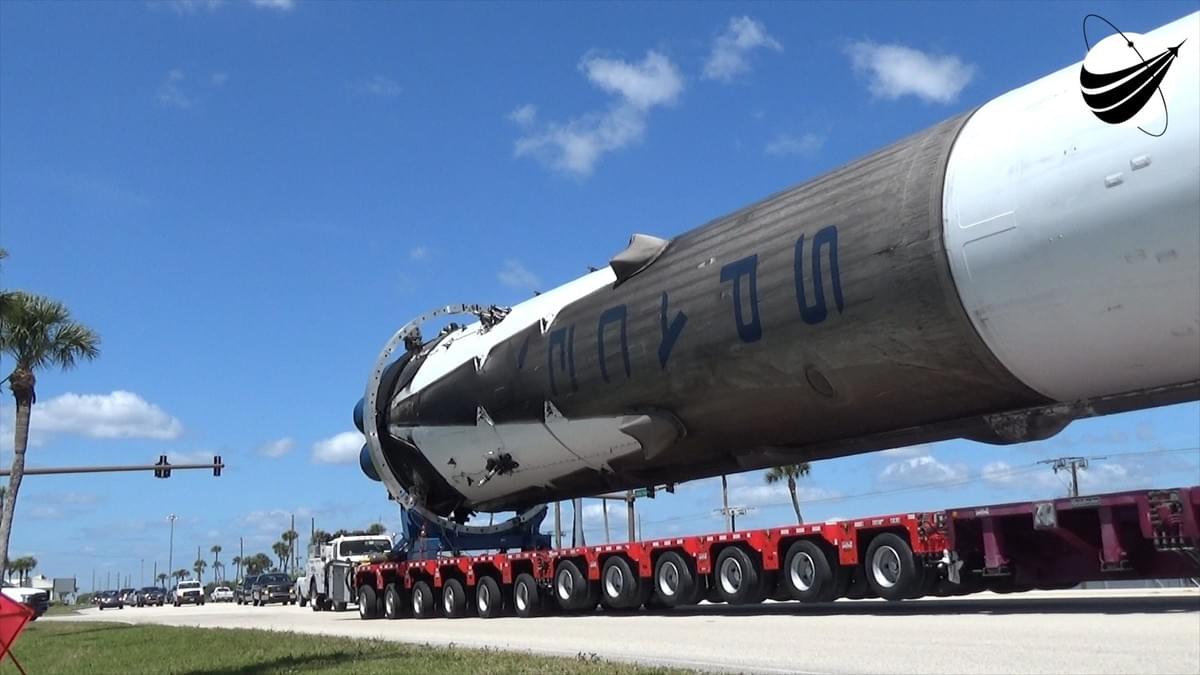
The turning circle for a rocket that's about the length of a football field tends to rule out a lot of the roads, and along the route it does have to take, a team has to take down all the road signs and traffic lights in every town to avoid taking them out. Once it's passed through, they have to put them all back up again. Sounds like slow going and a LOT of effort.
As an aside, moving parts around inside the SpaceX factory isn't easy either. Daniel, my guide worked in the logistics and tooling department. A lot of the ingenious ways of moving the stuff produced in the factory is moved around using custom stuff that he and his team creates.
6. Think like Martian
SpaceX engineers are already thinking ahead to our interplanetary future. On Earth we take advantage of our considerable fossilised plant and dinosaur deposits which form the kerosene used as rocket fuel. But the dinosaurs never made it to Mars (incidentally a prime example of a top-of-the-food chain species dying out scenario that prompts the kind of thinking that we need to populate multiple planets in the first place - it's a question of when not if a similar impact event happens on earth).
A lack of Martian dinosaurs means a lack of kerosene, which means a lack of ability to refuel and send ships back. Moreover, it also means a lack of oil in general, which means we have to get a bit more creative about our energy sources and the way we would make things if we successfully got people to Mars. It's not practical to take a lifetime supply with you.
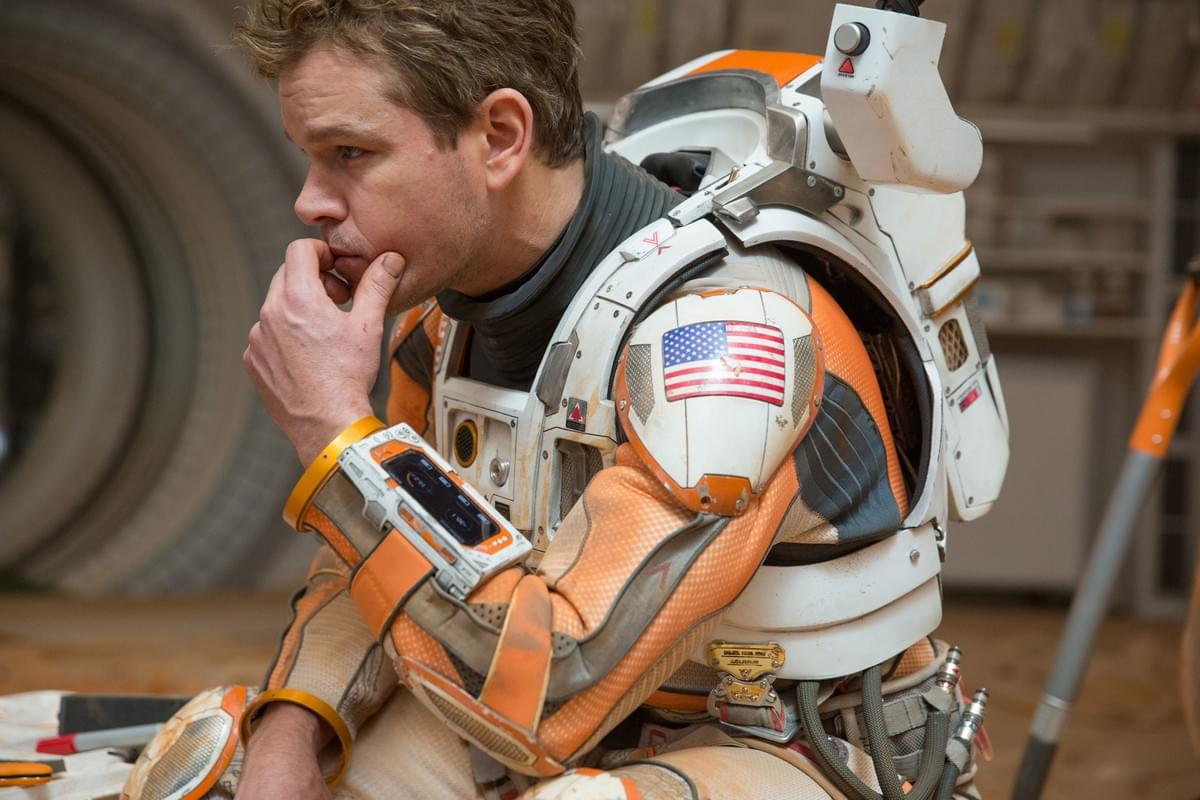
SpaceX are working on a different propellant system for its Interplanetary Transport System. It moves away from the previous kerosene/liquid oxygen combo and instead works on methane and liquid oxygen. Across five main criteria — vehicle size, cost of producing, reusability, the ability to produce on Mars itself, and the ability to transfer it to and from the spacecraft using mobile propellant tankers it stood out as a winner to Musk and the SpaceX team.
Another big hang up is spare parts. Things break, but you can't very well take a spare everything with you to Mars in case that happens. Future Martians will have to be able to produce their own widgets. The answer? 3D printing. Instead of bringing a ton of stuff, take a printer that will work off materials naturally found on Mars and you can make pretty much any part you can imagine.
Finally, SpaceX have even gone on to think about how you make things on Mars. Most arc welding techniques require some form of substrate in order to bind things together, something that again may not be available on the red planet. Instead, the engineers have worked on perfecting friction stir welding for use on the rockets, which is basically rubbing two materials together until they fuse together. No extra materials required and it creates a smoother bond less susceptible to structural stresses.
7. It's not (just) rocket science
If the above sounds extremely cool (lets face it, it is) and you're ready to sign up for a SpaceX job, there's a lot on offer. The lions share of the jobs on offer are to engineers - software engineers, hardware engineers, structures, propulsion, test and launch, avionics... the list is pretty long and varied and will span evertything from design to manufacturing to operations. However, it's not the only way in - an organisation like SpaceX needs HR, Business Development, cleaners, chefs and all sorts of miscellaneous support.
However, there are a couple of things you need to know.
SpaceX is like Special Forces… we do the missions that others think are impossible. We have goals that are absurdly ambitious by any reasonable standard, but we’re going to make them happen. We have the potential here at SpaceX to have an incredible effect on the future of humanity and life itself. — Elon Musk
First, it's going to be tough. In Musk's own words, it's like the special forces. They only take the best of the best. Second, if you're not an American citizen it's even tougher. I was told that because of the rules around the government contracts SpaceX has secured, recruitment outside of the US is only allowed if you truly fulfill a special skill set that can not be found domestically. That's not to say it's impossible - but it's very tough, and probably not getting any easier with President-Elect Trump's plans to restrict foreign workers.
Another thing you might want to bear in mind is that whilst SpaceX employees are top of the league tables in terms of deriving meaning and purpose from what they do, it's also a very demanding and high pressure job with relatively low pay compared to similar tech roles in comparable companies.
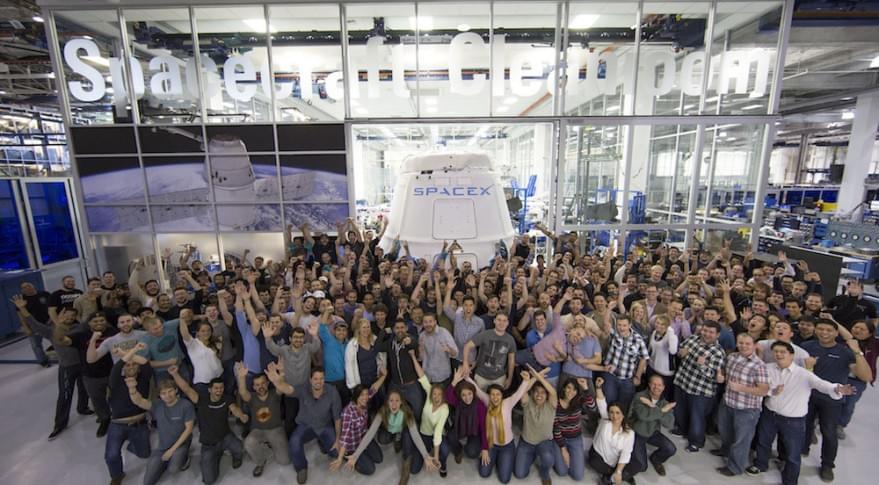
Having said that, I'm a firm believer that you do what you're passionate about, and what matters. Chasing money isn't the way to a fulfilling career. SpaceX is a testament to me about what engineering is really about. It's not stuffy, dry and boring. It's revolutionary, it's innovative, and it's changing our world in ways we can't fully imagine.
If I wasn't too busy working in just as demanding and meaningful role to make energy more affordable, reliable and accessible to everyone I'd sure as hell be considering helping us bring the stuff of sci-fi from a distant future right into the present.